Economic Performance
Against the backdrop of cumulative external influences, in 2021 we saw a gradual recovery of the Company’s financial performance to pre-pandemic levels. A recovery in global demand and OPEC+ regulation of the oil market have been the key drivers for oil prices increase. Timely actions in response to external challenges has allowed the Company to achieve better performance than we forcasted.
The Company’s net profit was 1,197 bln tenge in the reporting period.
Furthermore, as one of the largest taxpayers in the geography of operation, KMG makes its contribution to the national budget in form of taxes and other payments. In 2021, the Company paid 787 bln tenge in taxes and other obligatory payments to the budget.
The Company also employs over 55 thousand people in the country, providing them with steady remunerations along with social assistance for them and their families. In 2021, the Company paid 54 bln tenge of social and pension contributions for its employees.
Participation in domestic manufacturer support programmes and increasing the local content in procurements remain the KMG’s priorities. At the end of 2021, the total volume of goods, works and services procured by KMG Group (excluding KTG) from Kazakhstani companies was 1,216 bln tenge. The local content share in procurements was 78 %.
Planning and performance of the KMG’s Business Plan and Budget plays an important part in the Company’s value increase and reinforcing its financial stability for all stakeholders. The KMG planning is aimed at provision of medium-term (5-year) and current (for one year) planning of the KMG activities according to priorities and goals defined in the Development Strategy
Formation and approval of the consolidated and separate Development and Budget Plan of KMG is regulated by the Rules for formation, approval, adjustment and monitoring of the JSC NC “KazMunayGas” Development Plan. The Consolidated Business Plan includes the SDE plans for 5-year period and is regulated by the Plan for development, approval and monitoring of business plans and budgets of JSC NC “KazMunayGas” SDEs. The KMG’s Development and Budget Plans are formed in the automated planning system according to requirements of the approved corporate accounting policy of KMG and International Financial Reporting Standards (IFRS).
The KMG Management monitors the Business Plan performance on the basis of monthly, quarterly and annual management reports.
In the course of its operating activities, KMG makes annual substantial contributions to improve social and economic potential of the country and develop the regions of the Company’s operation.
The below economic performance figures provide a picture of the Company’s contribution to the national economy.
Created and Allocated Economic Value
Indicator |
UoM |
2019 |
2020 |
2021 |
Allocated economic value |
||||
Total income |
bln tenge |
7,970 |
5,202 |
6,743 |
Allocated economic value |
||||
Total expenditures |
bln tenge |
6,812 |
5,030 |
5,897 |
Unallocated economic value |
||||
Profit |
bln tenge |
1,158 |
172 |
1,197 |
Total income is the total revenue and other income in the consolidated income statement..
Total expenditures is the total expenditures and expenses in the consolidated income statement.
Indicator |
UoM |
2019 |
2020 |
2021 |
Other taxes and payments (excluding CIT) |
bln tenge |
1,360 |
1,068 |
1,440 |
Other taxes and payments (including CIT) |
bln tenge |
1,522 |
1,156 |
1,551 |
Income tax paid |
bln tenge |
162 |
88 |
111 |
Payments to capital providers |
bln tenge |
318 |
331 |
306 |
The data was received from the consolidated cash flow report (direct method) of KMG for 2021.
Payments to capital providers consist of Dividends paid to the shareholder, Dividends paid to the non-controlling participation interest, paid Remuneration and Distributions in favour of NWF Samruk Kazyna JSC.
|
UoM |
2019 |
2020 |
2021 |
Capital investments (per accrual method) |
bln tenge |
505 |
454 |
414 |
KMG did not received any financial aid in monetary terms from the Government in the reporting period and does not make any donations for public/political use.
Employee Pension Plans
In accordance with the national law, the pension savings of citizens are kept in the Unified Pension Savings Fund. The Company, in its turn, in accordance with the Collective Agreements of companies, fulfils additional obligations for social assistance to the retirees, according to which the employees retiring due to achievement of retirement age as well as after retirement, receive social assistance in the form of financial aid on the national and state holidays of the Republic of Kazakhstan, on anniversaries, in the form of health resort treatment vouchers with partial cost compensation and other. In 2021, financial assistance to the retirees of the Company was provided for a total amount of over 2 bln tenge.
Some of KMG companies have an early retirement plan for employees approaching the retirement age, allowing to pay them compensation in case of mutually agreed termination of employment; employees who have reached the retirement age can receive compensation upon termination of employment.
Indicator |
UoM |
2019 |
2020 |
2021 |
Social expenditures and compulsory pension contributions |
bln tenge |
52 |
53 |
54 |
KMG’s Tax Accounting Policy
NC “KazMunayGas” (hereinafter, KMG) Group, KMG has developed and implemented a Corporate Tax Accounting Policy (hereinafter, Corporate TAP).
The Corporate TAP was developed in accordance with requirements of the RoK tax laws in interconnection with International Financial Reporting Standards (IFRS), the RoK Law On Accounting and Financial Reporting, other RoK legislative acts and international contracts ratified by the Republic of Kazakhstan as well as internal documents regulating activities of KMG/ subsidiary. The Corporate TAP provisions are a commercial and tax secret of the KMG Group.
In the event of any conflicts between the provisions of the Corporate TAP and norms of the RoK tax legislation or international contracts ratified by the RoK, the tax legislation standards or the corresponding international agreement standards are applied.
KMG and all its subsidiaries are governed by the Corporate TAP, except for the subsidiaries:
- Performing subsoil use operations as a part of the production sharing agreement that provides a special stable taxation regime
- Where KMG owns less than 50% of the majority shareholdings (participation interest)
- Registered outside the RoK as well as the KMG branches and its subsidiaries’ branches registered outside the RoK.
The Corporate TAP’s goal at achieving the tax accounting uniformity in order to form in the reporting the most complete, objective and accurate information taking into account the organisational and industry-specific peculiarities of KMG and its subsidiaries.
The Corporate TAP’s objective is to reflect the specifics of tax accounting of the KMG Group in cases when the tax legislation:
- Contains the norms requiring or allowing to choose from several options or methods provided by the RoK Tax Code
- Establishes only common norms and does not ensure clearness and specifics in the ways of tax accounting, procedure for defining taxable items and the items related to taxation
- Requires to reflect certain conditions and provisions in the TAP.
The Corporate TAP is based on the following principles of the RoK Tax Code:
- Principle of Obligatory Taxation – KMG and its subsidiaries are obliged to timely and correctly calculate, withhold and pay taxes in full to the budget of the Republic of Kazakhstan.
- Taxation Equity Principle – operations of KMG and its subsidiaries cannot be subjected to double taxation with the same type of tax and payment for the same taxation unit for the same period
- Fairness Principle of KMG and its subsidiaries – it is prohibited to get benefit from illegal actions in order to ensure tax saving and tax payments reduction.
Based on the Corporate TAP, KMG, like all KMG subsidiaries, has developed and implemented KMG Tax Accounting Policy (hereinafter, KMG TAP).
Approval of the Corporate TAP and the KMG TAP as well as amendments to them is within the competence of the KMG’s Management Board.
Amendments to the Corporate TAP and KMG TAP are made in the following cases:
- Changes of the RoK Tax Code norms related to the procedure of tax accounting established by the Corporate TAP provisions
- Changes of the RoK Law On Accounting and Financial Reporting or the IFRS related to the procedure of tax accounting established by the Corporate TAP provisions
- The decisions made by KMG/subsidiary changing the methods and principles of accounting of the KMG Group, influencing the procedure of tax accounting, identifying the taxation items and/or the items related to taxation
- The decisions made by KMG/subsidiary leading to a change of procedure and principles of separate tax accounting of the KMG Group and other provisions, for which the RoK Tax Code has discretionary rules.
In other cases the changes in the Corporate TAP and the KMG TAP are introduced as required but not more than two (2) times a year.
KMG’s tax planning approach takes into account the specifics of KMG’s business activities and social impacts of this approach, which are fully consistent with JSC NC “KazMunayGas” Development Strategy for 2022-2031.
KMG’s Strategic Goals for 2022-2031 |
Link between the Taxation Approach and Strategic Goals |
Sufficient resource base to support KMG’s growth |
Fiscal incentives from government authorities |
Increasing efficiency of KMG’s value chain |
Negotiations with the state regarding further optimisation of the tax burden for mature fields to increase production at such fields |
Business diversification and product portfolio expansion |
Changes in the tax environment and possibility of obtaining/extending tax exemptions and preferences |
Sustainable development and progressive reduction of carbon intensity of operations |
Settlement of taxation procedure by obtaining clarifications from the tax authorities and amending tax law where necessary |
KMG’s Development Strategy is approved by resolution of KMG’s Board of Directors.
For more detailed information about the Company’s taxes (207-4) see 2021 Tax Report www.kmg.kz/eng/investoram/reporting-and-financial-result
Tax Administration and Control, Risk Management
Risk management in KMG prevents risk events that affect achievement of strategic and operational objectives, and limits their impact when they occur. Risk management is an integral part of KMG’s strategic planning and corporate governance process and support of financial stability.
The approach to managing risks, including tax risks, is set by the corporate risk management system (CRMS).
KMG has integrated the corporate risk management system (CRMS) into the company’s key business and management processes. CRMS aims to achieve an optimal balance between the KMG’s growth in value, profitability and risk.
CRMS is a key component of the corporate governance system aimed at timely identification, assessment and monitoring of all material risks (including tax risks) and adoption of timely and adequate risk mitigation measures.
The CRMS Policy of KMG and its subsidiary and dependent entities (SDEs) applies to all of the KMG’s activities.
Risk Management Process
CRMS is designed to provide a consistent and clear framework for managing the risks associated with KMG’s operations. KMG has built a vertical risk management process and functioning of risk management system at all levels of management, starting from the top level (KMG) to the line level (production business unit of SDE).
Each officer ensures that risks are properly considered when making decisions.
Risks are assessed using qualitative and quantitative tools that take into account the likelihood and impact of the risk.
CRMS is implemented through seven interrelated processes, integrated into KMG Group’s business management processes:
- Setting of goals (linking the strategic, medium-term and short-term planning objectives).
- Risk/risk factor identification (determining the exposure of all KMG Group’s activities, business processes to risks, the occurrence of which could adversely affect the ability to achieve planned objectives and goals).
- Risk/risk factor assessment and analysis (assessment is done to determine the extent to which risks/risk factors affect achievement of KPIs). Production/non-production risks and their corresponding risk factors are analysed by probability of their occurrence (likelihood of realisation) and degree of impact (potential damage).
- Risk management (the process of developing and implementing the measures to mitigate the adverse effects and/or likelihood of inherent risks and their corresponding risk factors or to obtain financial compensation upon occurrence of losses related to the risks of KMG Group operations).
- Monitoring and reporting (monitoring the changes in risk parameters and effectiveness of risk management measures and control procedures. Monitoring is performed by KMG’s Risk Management and Internal Control Service, a quarterly risk report consolidated with coverage of KMG SDEs is submitted to the Board of Directors).
- Informing and communication (allows to provide the risk management process participants with reliable and timely risk information, raises awareness of risks, methods and tools to respond to risks. The relevant information is identified, recorded and made available in a form and within time that enable the employees to perform their functions effectively).
- Internal environment (implementation of the above components of the risk management process promotes a risk culture within KMG Group, based on establishing an appropriate “tone at the top”, a high level of risk awareness and knowledge, responsibility of risk/risk factor owners, proactive risk management and timely reporting. KMG is committed to building an adequate organisational structure of CRMS that promotes effective corporate governance, ensuring appropriate segregation of duties, powers and responsibilities for identification, assessment, management and reporting of risks).
Interaction with the Board of Directors
The following documents are submitted to KMG’s Board of Directors at least once a year:
- proposals on the Company’s risk appetite;
- consolidated Risk Register;
- risk map;
- Action Plan for management of the Company’s risks.
In addition, a quarterly risk report (consolidated with coverage of KMG’s SDEs), including tax risks, is submitted to KMG’s Board of Directors for review and discussion in due course in its entirety. The Board of Directors takes appropriate measures to bring the current risk management and internal control system (RM&ICS) in line with the principles and approaches established by the Board of Directors.
The main tax risks of the Company may be:
- Ambiguous interpretation of the tax and customs laws.
- Incorrect preparation of tax reporting and customs goods declaration.
- Untimely provision of tax statements.
- Risks related to transfer pricing.
- Taxation of controlled foreign companies (inclusion of the CFC’s consolidated profit into the KMG’s taxable income).
- Non-resident taxation (individuals under the contracts with non-residents).
The main risk factors (causes) in the Company may be:
- Internal factors:
- Poor tax administration in KMG SDEs;
- Untimely provision of/failure to provide documents and information to the Accounting Office by the programme administrators;
- Errors when preparing tax statements and customs goods declaration;
- Insufficient knowledge of the tax law;
- Inappropriate tax review of agreements/contracts;
- Untimely preparation/insufficient substantiation of tax preferences/changes in the tax law.
- External factors:
- Ambiguous interpretation of the RoK tax law.
- Retrospective changes to the RoK tax law;
- Errors of the tax authority IT infrastructure;
- Ambiguous interpretation of the transfer pricing law.
The main preventive measures at the Company are:
- Regular monitoring of changes in the RoK tax law, and their consideration in the work.
- Participation of employees in seminars, forums, self-education in tax law and transfer pricing.
- Follow up of tax accounting and tax statements;
- Regular reconciliation with tax authorities.
- Provision of tax expert opinions on major deals (approval of draft contracts).
- Obtaining explanations from state revenue authorities regarding tax, customs and transfer law.
- Audit of tax statements (as required).
- Correspondence with authorised bodies to get explanations of regulatory legal acts.
- Defending the company’s interests in court.
- Analysis of risks of price deviation in major transactions (TC).
- Monitoring of draft revisions to the transfer pricing law initiated by the state authorities.
Stakeholder Engagement and Management of Tax-Related Problems
KMG is included in the list of major taxpayers subject to tax monitoring in accordance with tax legislation.
KMG regularly analyses problematic issues of tax legislation application in the KMG Group with further development of proposals to amend the legislative acts as well as initiates amendments into the RoK legislation in order to create favourable conditions for taxation of the KMG Group, systemic improvement of tax legislation, customs legislation of the Customs Union and the RoK, the RoK transfer pricing legislation, and increase of operating efficiency and value of KMG as a whole.
The relations and interaction with the state authorities are formed under the RoK Tax Code standards via business correspondence in order to determine a correct tax policy, participation in the meetings, discussions organized by the state authorities and shareholders and industry associations.
Protection of the KMG Group’s interests by improving the legislation includes:
- development of proposals (including substantiation, presentations and calculations) on improvement of tax legislation;
- consideration and provision of opinions on the draft legal and regulatory acts developed by the corresponding state authorities as a part of execution of tax legislation and subsoil and subsoil use legislation;
- support of legislative initiatives of KMG Group by direct participation in advisory bodies of the industrial associations (Association of Taxpayers of Kazakhstan (ATK), KAZENERGY, National Chamber of Entrepreneurs of the RoK “Atameken” (NCE), working groups with involvement of the state authorities of the Republic of Kazakhstan and RoK Parliament.
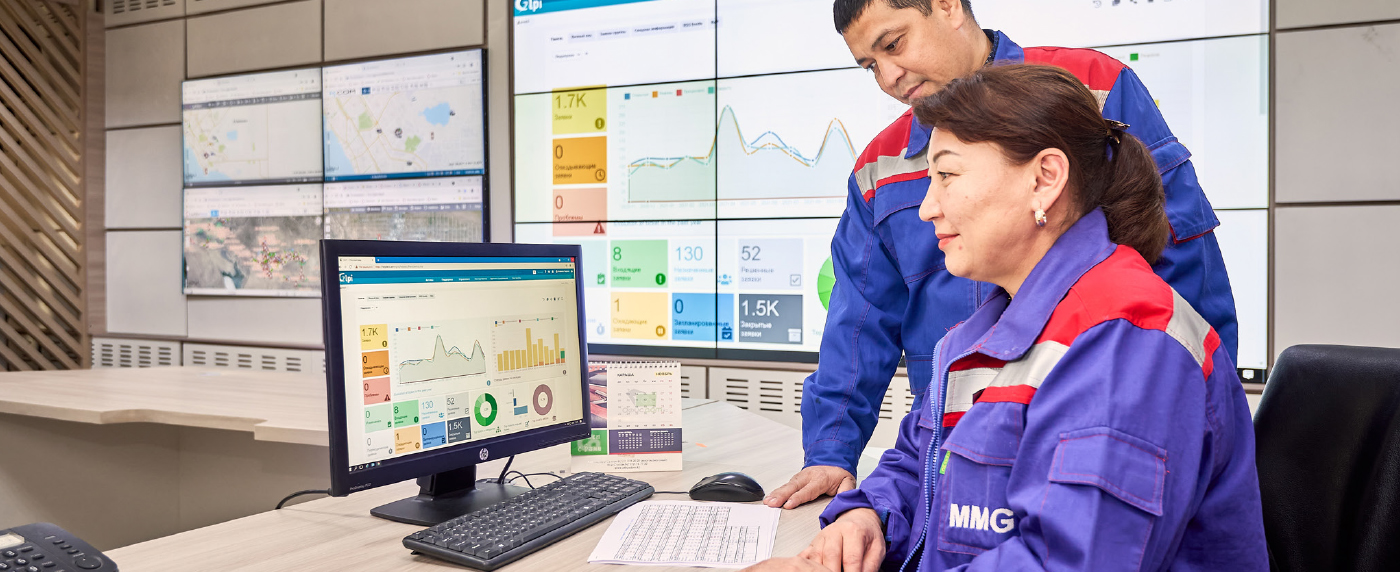
Implementation of Investment Projects
KMG is a national leader of oil and gas industry of Kazakhstan with full integration at all stages of the value-added chain. KMG has a stable platform for its long-term sustainable development as a leader of oil and gas industry and a vertically integrated company. KMG assets include the full cycle of hydrocarbons added-value chain, consisting of exploration, extraction, transportation, refining and marketing. The activities are performed in Kazakhstan and Romania.
As a part of the above-mentioned businesses, KMG implements over 50 investment projects aimed at increase of hydrocarbon reserves, creation of new productions, and expansion and renewal of the existing productions.
Implementation of the following investment projects contributes to sustainable development of Kazakhstan:
Projects of gasification of the regions of the Republic of Kazakhstan, modernization of trunk and gas distribution networks, increasing the resource base
In 2021, the successfully completed investment projects included:
- Gasification of Almaty, upgrade, revamp of gas distribution networks of Almaty The project contributes to improving the environmental situation in Almaty and has provided gas to about 4,000 new customers, more than half of whom had been connected to the gas distribution network by the end of 2021, with the remaining households also having access to gas and will be connected as soon as possible. Since the start of the project, a total of 265 kilometres of new gas pipelines have been built, 94 kilometres of existing pipelines have been reconstructed and 35 gas control cabinets have been installed.
- Construction of gas distribution networks of start-up complexes 1 and 2 of Stage 2 in Nur-Sultan Gas supply from AGDS-2 to Vostok main gas distribution station (MGDS) and Yugo-Vostok MGDS is provided as part of the 1st start-up complex, and gas supply from Vostok MGDS to the residential districts Internatsionalniy, Michurino, Kuigenzhar and to the boiler houses is provided as part of the 2nd start-up complex. In 2021, gas distribution networks with a total length of 100.581 km were built, 5 gas control units and 5 gas control cabinets were installed. The number of planned customers is 1,644. At the end of 2021, 71 customers and 1 utility company were connected in Internatsionalniy, Michurino and Kuigenzhar residential areas.
In 2021, work started on priority projects of KTG:
- Gasification of Sarsha Area and Warm Beach Resort Area Construction of a multifunctional hotel and tourist complex in Sarsha, Mangystau Region, is underway to develop the tourism industry as instructed by the President and the Government of the Republic of Kazakhstan. To provide natural gas for new consumers of the hotel and tourist complex in Sarsha Area and Warm Beach Resort Area, a branch gas pipeline from Zhanaozen-Aktau main gas pipeline with the length of 85 km was built in 2021 with installation of an automatic gas distribution station with capacity of 80,000 m³/hour. In 2022, it is planned to complete the construction of distribution networks to Sarsha and Warm Beach resort area with a length of 59 km and two gas control units.
- Construction of the loop line to existing Makat – North Caucasus main gas pipeline. In order to ensure stable gas supply to the population and large industrial facilities of Atyrau and Atyrau Region, prevent emergencies and provide uninterrupted gas supply to the special economic zone “National Industrial Petrochemical Technopark”, KTG plans to implement a project for construction of a looping line to Makat – North Caucasus gas pipeline during 2021-2023.
- Construction of 2nd string of Beineu – Zhanaozen trunk gas pipeline. Due to the planned increase in gas consumption in Mangystau Region, the capacity of Beineu – Zhanaozen trunk gas pipeline is insufficient to pump the projected additional gas volumes. In 2021, work began on reconstruction of Mangystau Region gas transmission system, which will improve the region’s energy security and throughput capacity to meet the growing demand for natural gas in the region. In order to solve the above tasks, KTG plans to build the second string of Beineu – Zhanaozen trunk gas pipeline between 2021 and 2023.
- Construction of a trunk gas pipeline from Kashagan GPF to Makat – North Caucasus TGP with compressor station. Also, in order to increase the resource base and gas export to the PRC, a project has been initiated for construction of a trunk gas pipeline from Kashagan GPF to the Makat – North Caucasus trunk gas pipeline with a compressor station. This project is a part of a large-scale project to build a gas processing plant, the Gas Processing Facility (GPF), at Kashagan field, with a processing capacity up to 1 bln cubic metres of raw gas per year. Construction and assembly works are currently underway, with completion scheduled for 2023.
The works under the following investment projects continued in 2021:
- Construction of Beineu – Bozoi – Shymkent trunk gas pipeline Wok continues under the investment project for construction of Beineu – Bozoi – Shymkent trunk gas pipeline with a throughput capacity up to 15 bln m3/year. The gas transported via this gas pipeline is supplied both to the population of the RoK regions and for export to PRC. Currently, all the main facilities of the gas pipeline, which provide the required (stated) capacity, have been commissioned. In 2021, Beineu gas metering station and stage 1 SCADA system were commissioned at the Bozoi – Shymkent section of the trunk gas pipeline. Turkestan compressor station built by Intergas Central Asia JSC has been bought out (a total of 2 out of 4 built stations have been bought out for 2021). In 2022, it is planned to complete the expansion of Beineu GMS and Bozoi CS and build the remaining stage 1 and stage 2 facilities (maintenance and operation areas, SCADA system and route road) and to buy out Aral compressor station built by Intergas Central Asia JSC to expand the gas pipeline capacity to 15 bln m3/year.
- Geologic Exploration Works at the Barkhannaya – Sultankuduk structure of Amangledy deposit The exploration team completed 3D seismic acquisition in 2021 on the area of 690 km2 and has now begun drilling of appraisal well No.B-5 at the Barkhannaya structure, which will result in estimation of HCs reserves.
- Production Team of the Amangeldy Gas Deposit Group Development Project The production team is continuing work according to the Work Programme and FEM, with Anabay field planned to be commissioned in 2022-2023.
- Gasification of three settlements (Zhitikara, Tobol and Bolshaya Churakovka) in Kostanai Region The project began in 2021 and involves gasification of certain districts of the town of Zhitikara and villages of Tobol and Bolshaya Churakovka. In 2022, it is planned to complete construction of high, medium and low pressure gas distribution networks to these settlements with a total length of 127.8 km. The project contributes to improving the environmental situation and will connect about 3,275 new consumers. In 2021, 52.4 km of gas pipelines were built and 3 gas control units were installed. 42 new consumers have been connected.
- Construction of high-pressure gas supply pipeline and gas distribution networks in Saimasai, Kainar, Enbekshikazakh District of Almaty Region (PK 1 and 2) It is planned to supply gas to consumers in Saimasai and Kainar settlements of Enbekshikazakh District of Almaty Region (1,150 houses, 36 social facilities) with perspective of further connection to gas transmission network of 25 nearby settlements of Enbekshikazakh District (12,144 houses, 288 social facilities and state-funded organisations). The Project involves construction of high, medium and low pressure gas distribution networks with a total length of 89.79 km. At the end of 2021, 13 km of gas pipelines have been built. The Project is scheduled for completion in 2022.
Oil transportation projects
Kenkiyak-Atyrau Oil Pipeline Reversal Project as part of the combined project “Stage 2 of Construction Phase 2 of Kazakhstan-China Oil Pipeline” will increase the capacity to 20 mln tonnes of oil per year. The project aims to ensure transport of up to 20 million tonnes of West Kazakhstan oil per year to POCR and PKOP and to increase oil export to PRC. The second start-up complex (process facilities of Aman OPS) was commissioned on 30 June 2021, which made it possible to transport oil in reverse. All complex facilities will be fully operational in March 2022.
- Oil and gas refining projects. Proving its commitment to best health, safety and environment (HSE) practices, in 2020 Atyrau Refinery continued to design and build new mechanical treatment facilities for the refinery under Tazalyq Project. Tazalyq Project includes upgrading of mechanical wastewater treatment facilities and reclaiming of Tukhlaya Balka evaporation ponds located on the left bank of Atyrau in order to meet environmental requirements of governing authorities. The environmental benefit from the new mechanical treatment facilities is the disposal of 8,000 m2 of open petroleum product evaporation ponds and recycling of 15% of treated wastewater in own production. The environmental effect from reclamation of the evaporation ponds is preventing the adverse impact on the atmosphere, groundwater, local flora and fauna. Subproject implementation terms: 1. Reconstruction of mechanical treatment facilities at Atyrau Refinery – 2019-2022. 2. Reconstruction of channel for effluents treated to standard quality and reclamation of evaporation ponds – 2019-2023.
- Construction of a new gas processing plant in Zhanaozen. Considering the maximum wear of the main process equipment, technical devices and utilities of the gas processing plant in Zhanaozen, significant risks related to safe labour conditions, compliance with environmental requirements, man-caused danger with environmental consequences, risks of gas disposal by subsoil users, risk of failure to provide the population of Mangystau Region with gas processing products. In 2021, pre-FEED and feasibility study were developed and submitted for the State Expert Review. In 2022, it is planned to sign an EPC Contract for construction of the plant, develop the DED, order equipment and start the construction and assembly works. Construction of the plant is planned to be completed at the end of the first half of 2024.
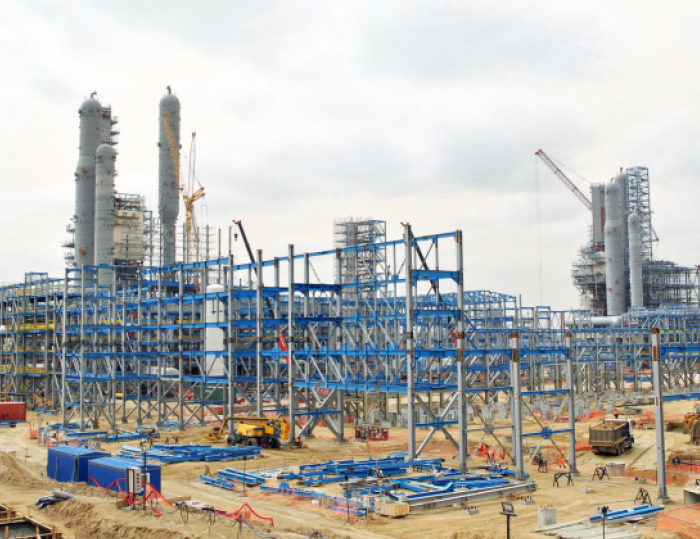

WATER SUPPLY PROJECTS
- KMG assists CITIC ENVIROTECH LTD with implementation of the project for construction of the formation water desalination plant at Karazhanbas field as well as utilities connection to the desalination plant. The current status of the utility networks connection is 98% and that of the plant is 80.5%. Also in 2021 and since the beginning of this year, all process equipment for the project has been delivered, except for the plant ventilation system and chemicals (in transit). The overall completion of the plant (PWRI) and commissioning is scheduled for the second quarter of 2022.
- KMG also implements the project to increase the throughput capacity of the Astrakhan – Mangyshlak water main and upgrade the worn out equipment to cover the existing deficit and future increase of water consumption in Atyrau and Mangystau Regions of the Republic of Kazakhstan. Stage 1 of the project will increase water feed capacity from 30,100 thous. m3/year to 68,388 thous. m3/year by the end of 2024. The project DED has now been developed and work has been done to secure project funding.
- KMG is implementing a project to build a seawater desalination plant with a main pipeline near the Kenderli recreation area with a capacity of 50,000 m3 per day according to the Comprehensive Plan for Mangystau Region Development. The purpose of this plant is to provide drinking water to the population of Zhanaozen to cover the existing water shortage. The plant construction is scheduled for completion at the end of 2024.
Procurement Practices
Ensuring effective procurement with commitment to meet the sustainable development principles is an integral part of KMG’s activities, which contributes to achievement of strategic and operational objectives.
KMG Group’s procurement philosophy is compliance with legal and internal requirements, transparency of procurements, development of fair competition and provision of equal opportunities for contractors. At the same time, KMG has undertaken a number of procurement initiatives in support of domestic producers under the Programme to Support Upgrade of Existing and Creation of New Production Facilities.
In order to achieve and improve the transparency and efficiency based on the most advanced international standards and techniques, the procurement procedures of KMG Group employ the Information E-Procurement System https://www.skc.kz/ru/regulations/ (hereinafter, IEPS), which provides unhindered access (with certain exceptions, primarily related to state secrets) to procurement information for all stakeholders, equal opportunities for all participants of procurements.
IEPS automates and standardises the entire procurement cycle (from the planning process to contract management), reduces the time required to complete the tasks and mitigates the impact of human error. E-procurement facilitates access to the market and thus contributes to greater efficiency, increased competition and reduced administrative burden and transaction costs.
In addition to public dissemination of procurement information relating to procurement procedures and procurement contracts, including information on invitations to tender and the conditions of contracts, IEPS enables early establishment and publication of requirements for participation in competitive procurement, including the selection criteria and tendering rules. At that, IEPS provides an effective system of internal control, including appealing the procurement results in case of non-compliance with rules or procedures set out in regulations.
In addition, IEPS is integrated with government databases, which saves resources for bidders: time, huge amounts of paper for preparing the tender documents, money for preparing the notarised copies of documents, postage for forwarding of documents, and travel expenses.
Total Procurement Volume
One important aspect of KMG’s procurement activities is reducing single-source procurements and increasing the share of competitive procurements. In this regard, accountability of the managerial employees of KMG and its subsidiaries and dependent entities (SDEs) is provided, including through target setting in the Key Performance Indicator (KPI) Chart of the managers.
Despite the desire to develop a competitive market, the share of non-competitive procurements within intra-group cooperation and/or through a single source significantly prevails, mainly due to lack of a competitive environment (e.g., oil transportation by trunk pipelines, oil refining at oil refineries in Kazakhstan, etc.) and the need to provide a social environment in the regions of deployment (e.g., procurement of oilfield services).
During the reporting period, the total amount of supplied goods, works and services (including annual and long-term purchases) was 1,216 bln tenge, of which 78% was local content.
Total amount of goods, works and services and local content share (bln tenge)
Year |
Goods |
Works and services |
Total |
|||
|
Total amount (bln tenge) |
Local content share, % |
Total amount (bln tenge) |
Local content share, % |
Total amount (bln tenge) |
Local content share, % |
2019 |
473 |
63 |
1,659 |
83 |
2,132 |
81 |
2020 |
472 |
71 |
1,354 |
86 |
1,826 |
82 |
2021 |
273 |
57 |
943 |
85 |
1,216 |
78 |
4% decrease in the local content in the goods procurement versus 2021 is due to divestment of KTG (gas purchase) from KMG in early 2021.
The above figures reflect the consolidated data for all KMG subsidiaries where fifty or more percent of voting shares (participation interest) are directly or indirectly owned or held in trust by KMG, and which are subjects of procurement procedures regulated by Samruk Kazyna JSC.
Pre-Qualification of Potential Suppliers
International procurement practices demonstrate extensive development of pre-qualification mechanism for potential suppliers. Continuous improvement of procurement based on the requirements and standards of Kazakhstan and international practices is one of the priorities for KMG.
Pre-qualification (PQ) is the assessment of potential suppliers for compliance with qualification requirements defined in accordance with the Standard19, carried out through questionnaire survey and audit.
The key goals of PQ are:
- arranging a simple, transparent and efficient process for assessing suppliers against set qualification criteria;
- supporting real local producers;
- improving the quality of procured goods, works and services (GWS);
- shortening the timeframes and simplifying the procurement procedures.
Pre-Qualification of Potential Suppliers Procedure (PPP)
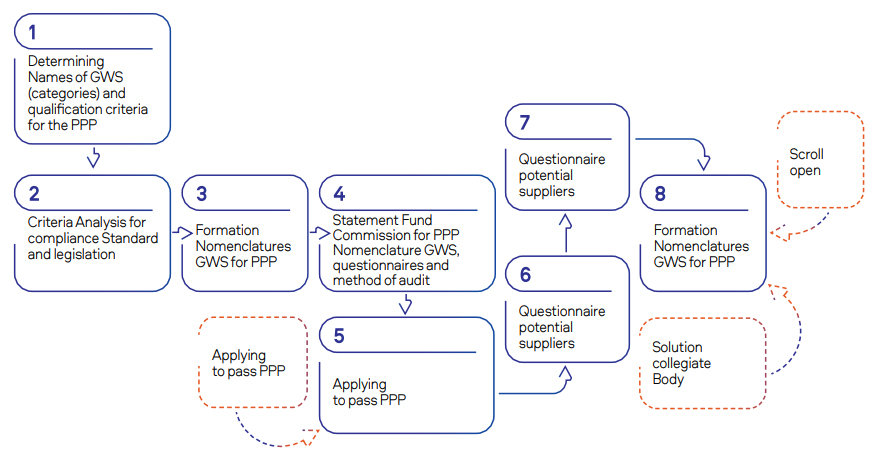
Category Procurements
Procurement category management is the process of developing an integrated approach to reducing the costs associated with procurement and use of goods, works and services included in priority categories.
Categorisation is done by grouping the goods, works and services into procurement categories based on common characteristics of the procured item and/or a single market of potential suppliers. Categories may include one or more items of goods, works and services. Categories with high level of costs, criticality, savings potential and manageability are identified as priorities.
Category management increases the potential for savings through more detailed analysis by developing and approving a category procurement strategy. This strategy is a document that defines the optimal approach to goods, works and services procurement based on maximum benefit in the long or short term. Procurement category strategies should include goals and objectives, analysis of the internal and external environment, procurement category management approaches, supplier development requirements, calculation of benefits and implementation plan.
Category management can significantly reduce the cost of acquiring and using goods, works and services by applying strategic planning, detailed analysis of procured goods and services and calculations of total cost of ownership, as well as by means of cross-functional cooperation with various business units. This procurement method is effective in that it ensures both quality and transparent pricing by working with reliable producers and suppliers.
Procurement category management includes:
- categorisation of procured goods, works and services and prioritisation of procurement categories;
- development (update) and approval of category procurement strategies for priority categories;
- implementation of procurement category strategies;
- monitoring of procurement category strategies implementation;
- supplier development.
For KMG, category procurement volume in 2021 amounted to 117,436.49 mln tenge. This method is planned to achieve an economic benefit of 13,527 mln tenge in procurement of goods, works and services included in priority categories.
Volume and benefits of category procurement in 2017-2021:
Indicator |
2019 |
2020 |
2021 |
Volume of categoryprocurements, mln tenge |
41,531.68 |
49,716.04 |
117,436.49 |
Benefits of procurement category management, mln tenge |
4,101.81 |
7,011.23 |
6,494.76 |
Import Substitution
As a company representing the state’s interests in the oil and gas industry, KMG is actively working on import substitution under the state programme to support upgrade of existing and creation of new production facilities through off-take agreements. The key objective of the programme is supporting the private entrepreneurs initiating new production facilities and technological upgrading in order to manufacture the products demanded by Samruk-Kazyna JSC Group companies.
The off-take agreement mechanism provides for implementation of import-substitution projects with a condition of future purchase and supply of commodities to be produced as a result of such implementation.
Commitment to Sustainable Procurements
KMG’s sustainable development principles are reflected in its cooperation with contractors based on legality and transparency, compliance with contract conditions, incorruptibility and intolerance of any instances of corruption, and in selection of contractors based on a combination of the following factors: best price, quality and conditions, and contractor’s goodwill.
At that, KMG requires the contractors to makes reciprocal commitments to comply with applicable laws, treat employees fairly, not use child labour, ensure safe working conditions, protect the environment and adhere to other principles of ethical conduct.
These conditions are included in conditions of contracts concluded by KMG with its contractors in order to respect labour rights and create favourable working conditions for citizens of the Republic of Kazakhstan, protect children’s rights and ensure environmental safety. According to KMG, these measures will help reduce the number of cases of misconduct by companies cooperating with KMG.
When procuring goods, KMG also sets requirements for potential suppliers to provide certificates of compliance with the quality management system.
Cooperation with Contractors and Ensuring the Social and Labour Rights of Contractors’ Employees
In order to comply with the established guarantees of labour relations for contractors’ employees, the Standard Regulations for Cooperation of SDEs with Contractors Operating at KMG Facilities have been approved and are currently being introduced by KMG in SDEs. The Regulations are binding for SDEs in the course of execution and monitoring of contracts with the contracting companies that have their own personnel and will form a part of contracts between SDEs and contracting companies. The main objective of the Regulations is ensuring social and labour rights of the contracting companies employees.
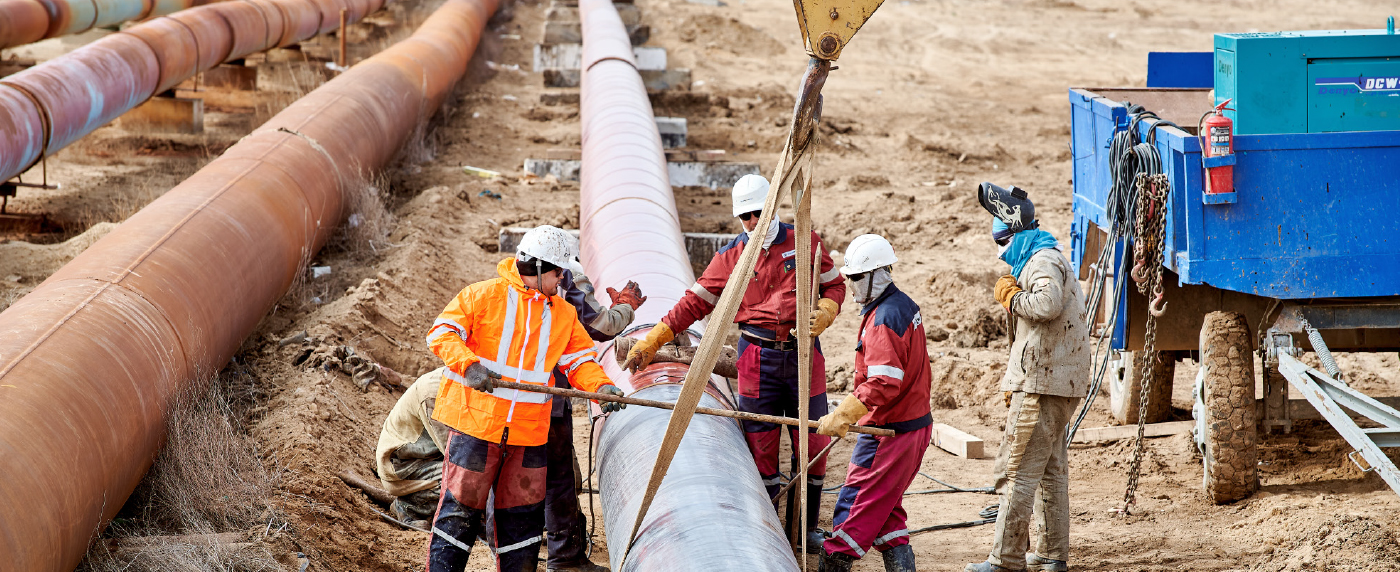
The situation in SDEs is under constant monitoring by KMG and remains relatively stable. Being aware of the potential adverse effects caused by contractor downtime during the pandemic, KMG took steps to support contractors to the maximum extent by allocating workloads to maintain personnel employment, keeping a balance between the company’s interests and socio-economic situation.
To increase the remuneration of contractors’ employees, KMG recommends SDEs to set requirements for contractors at the contracting stage so that monthly tariff rates/salaries of contractors’ employees are not lower than 70% of the monthly tariff rates/salaries of similar occupations at KMG SDEs and implement minimum social package. KMG Group has allocated 3.8 bln tenge in 2021 for these purposes.
Anti-Competitive Conduct
During the reporting period, 26 administrative cases were initiated against KMG Group companies for violations of antimonopoly laws (all against SDEs).
Of these, 1 administrative case was partially resolved in favour of SDE, 12 administrative cases were resolved not in favour of SDE and 13 cases are pending. .
There are no civil cases relating to anti-competitive conduct, anti-trust or anti-monopoly law violations.
Social and Economic Compliance
There are no civil or administrative cases where the subject matter of the litigation/violation was non-compliance with laws and regulations in the field of social and economic regulation or disputes with local communities.
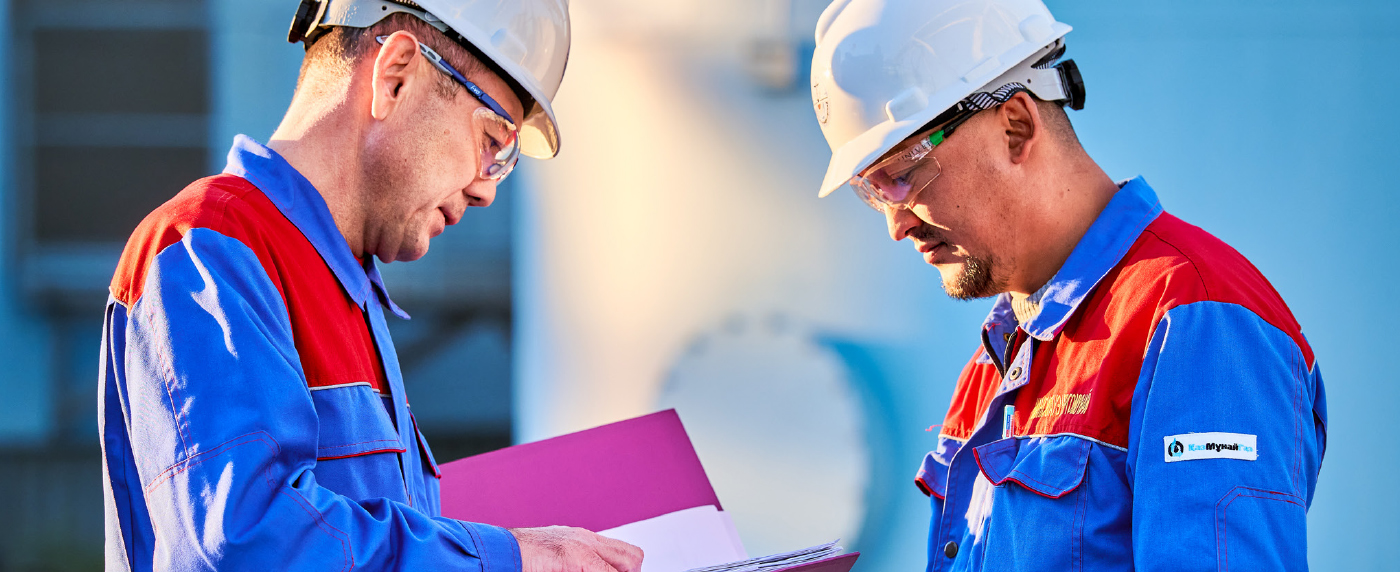