Digital Transformation Progress
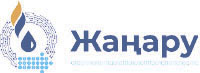
Results of 2021
Digital transformation is set as a cross-cutting objective of KMG’s new Development Strategy 2022-2031, which identifies sustainable development and progressive reduction of carbon intensity of operations as one of its goals. To achieve this, the transformation includes projects to develop a lean manufacturing culture among KMG Group employees. For example, a Lean 6 Sigma (LSS) implementation project trains and certifies employees of KMG Group’s production companies. LSS method helps to involve the personnel in a continuous effort to improve the company’s performance while optimising resources. The programme encourages the continuous search for and implementation of simple, low-investment, short-term projects to reduce operating expenditures. A total of 13 LSS projects were implemented in oil production in 2021. Most of improvements concerned increasing the time between well workovers and reducing equipment repairs.
LSS project has previously been successfully implemented at oil refineries. Since 2016, 156 projects under the programme have been implemented at the refineries. 89 employees have been trained and certified. Qazaqstan Project Management Awards recognised Lean 6 Sigma Project in the Oil Refining and Petrochemicals as the best project of 2021 in Kazakhstan.
The 3rd place winner in the competition was the Computer-Aided Simulators (CAS) implementation project at Atyrau Refinery (AR) and Pavlodar Oil Chemistry Refinery (POCR), and PetroKazakhstan Oil Products (PKOP) is also introducing Computer-Aided Simulators (CAS). It solves similar sustainable development tasks. Using digital twins, the refinery unit operators simulate emergency and routine situations, which minimises operation disruptions due to human error and enhances workplace safety.
A total of 13 AR, 9 POCR and 1 PKOP process units are planned to be equipped with CAS.
Sustainable Development Goal (SDG) 9 – Industrialisation, Innovation and Infrastructure is pursued by ABAI Information System Development Project. This fully domestic digital product is being implemented by KMG Engineering LLP. The system will integrate all production data from KMG Group’s Upstream companies, with the ability to verify and analyse it using artificial intelligence and machine learning tools, as well as instant visualisation.
ABAI IS will consist of about 20 autonomous modules, each addressing a specific production problem of KazMunayGas subsidiaries. In 2021, 5 pilot modules of the system were commissioned: ABAI Database, Visualization Centre, Process Mode, Downhole Pumping Equipment Selection and Complication Monitoring. They already demonstrated good results at the testing stage.
For example, the algorithms of the Process Mode module analyse well performance and calculate well potentials, which enables a more efficient allocation of planned oil production between wells and reservoirs each month and thus rationalises field development. The module is based on actual data from Kazgermunai’s (KGM) internal database and takes into account the current and potential downhole pressures as well as productivity factors. Based on these values, the maximum possible amount of oil under the available geotechnical conditions is calculated. During the algorithm’s testing period from May to October 2021, 13 KGM’s wells increased production by 560 tonnes.
At the second stage of ABAI project, 12 more modules will be developed to digitise key oil production processes, from exploration and drilling to operation and economic impact assessment. Full implementation of the system is expected to cut KMG SDEs’ operating expenses by 2-3%.
Several SDGs at once are covered by the project launched in 2021 to establish a Multifunctional Shared Service Centre (SSC) for KMG Group, which will carry out routine and transactional processes of bookkeeping and tax accounting, treasury, human resources management, administration and documentation support. This will reduce the burden on key businesses and free up the time of production company managers for their direct tasks. The service model of SSC’s engagement with businesses will ensure high quality and speed of service delivery. Increased labour productivity through standardisation and automation of routine processes will enable a more efficient allocation of resources within KMG and introduction of new processes (SDG 8 – Decent Work and Economic Growth).
Another advantage of a SSC is an increased speed of information receipt throughout the holding, including instant access to information on liquidity, receivables, personnel movements and other critical management data under unified standards. A high rate of innovation introduction will be ensured by making the Shared Service Centre the main functional customer of IT architecture for the functions listed above and it would be able to centrally implement and replicate the advanced solutions available on IT market (SDG 9).
The availability of new digital services in SSC will have a positive impact on the working conditions and quality of life of personnel, customers or suppliers. The digital literacy of company employees and ordinary people in the regions where KMG operates will also be improved (SDG 10 – Reduced Inequality).
Finally, the establishment of SSC involves a full transition to electronic documents for the entire life cycle of certain business functions (SDG 13 – Climate Action).
Plans and Objectives for 2022
Transformation will continue to support the Sustainable Development Goals and KMG’s Development Strategy through promotion of digital technologies in exploration in the next period. Priorities include seismic and well surveys using machine learning and artificial intelligence, creating a corporate digitalisation template using new assets (digital twin).
The focus of Lean 6 Sigma programme will also shift to Lean Digital, i.e. LSS tools will be used to develop business initiatives aimed at reducing losses in production processes through the use of customised digital solutions.
The issues of ecology, health and safety, production reliability, cost reduction and improving the digital literacy among KMG employees and Kazakhstani youth through various training programmes and internships remain on the transformation agenda.
Digitalisation Projects in the Oil Refining and Petrochemicals Division
Computer-Aided Simulators
In order to improve the quality of work of personnel in routine and non-routine situations, increase the reliability of unit operation and prevent unscheduled shutdowns, a project of Implementation of System for Training and Certification of Production Personnel at RoK Refineries through Introduction of Computer-Aided Simulators (CAS) is being implemented from 2019. The goal of the project is developing a dynamic process model based on a mathematical process model and a visualisation of the refinery’s process unit. Visualisation is made by: 1) Full replication of the distributed control system (DCS) interface and logics 2) Display of real equipment in 3D or panoramic interface format. Using CASs, the unit operators regularly work out the emergency and routine situations (start / shutdown) in simulated conditions.
During the modernisation and upgrade of PKOP, the CASs were introduced at catalytic cracking and heavy residue units (RFCC), cat-cracked gasoline hydrotreatment (Prime G+), saturated and unsaturated liquefied hydrocarbon gas sweetening (Merox), short-cycle adsorption (SCA-2) and sulphur recovery units.
The CAS project initiated in 2019 covers eleven AR process units, nine POCR units and one PKOP unit.
During the project implementation in 2019-2020, CASs were commissioned at the delayed coking, naphtha isomerisation and splitter, diesel hydrotreating and paraffin hydrotreating units of POCR, catalytic reforming unit of PKOP, catalytic cracking (FCC), catalytic reforming (CCR) units and aromatics (PX) production complex of AR.
In 2021, the computer-aided simulators were introduced at 4 AR units (Sulfrex, Naphtha HT, Prime D, Parisom) and at the Sulphur Production Complex at POCR.
Rules for using CASs in the training and knowledge testing of refinery process personnel have also been developed and approved. Instructors have been appointed at the refineries, responsible for running the simulators, conducting training sessions, developing scenarios and testing knowledge about CAS.
Regular training sessions are held for refinery personnel using CAS in accordance with approved training plans, training schedules and prepared scenarios for emergency and routine situations.
Advanced Process Control System
In order to solve the business task of process control automation at the unit, an Advanced Process Control System (APCS) has been put into commercial operation on a pilot basis at ELOU-AT-2 primary refining unit of AR. The system is known worldwide as Advanced Process Control (APC).
The function of APCS is that, like an ’autopilot’, it steadily maintains the unit process mode within the specified limits. It automatically monitors constant parameters of unit load, column and heater temperatures and quality parameters of the streams leaving the unit. This reduces the influence of the human factor in process control.
By introducing APCS at AT-2, the spread in fuel quality was reduced by 67% for gasoline and by 73% for diesel fuel. APCS increases the gasoline yield by getting as close as possible to the end boiling point of gasoline, and the diesel yield by getting closer to the target pour point.
The project lasted about a year from April 2019, including AT-2 inspection, design, equipment installation, testing and integration of APCS with the distributed control system (DCS). AR’s subject matter experts and unit operators have been trained in using the system. The system is in operation around the clock and is now as much an integral part of the unit control as the DCS.
Introduction of APCS at AT-2 unit has resulted in a significant effect. An increase in the gasoline and diesel yield by 0.32-0.36% (to 6,500 tonnes) amounted to about 350 mln tenge a year in monetary terms.
Following the success of this pilot, the system will be introduced at the Atyrau Refinery’s AVT-3 unit in 2021, and at the catalytic cracking unit in 2022 and then at other Atyrau Refinery units. In 2022-2023, it is planned to replicate APCS at PKOP.
3D Layout. Refinery Engineering Data Management System
The project of Creating the Digital Layout and 3D Refinery Model is being implemented in order to create a digital layout of the refinery with high accuracy as the basis for a digital twin.
The project involves:
- laser scanning of all facilities;
- digitisation of all technical documentation of the refinery;
- creation of a 3D digital model of the refinery based on point clouds;
- implementation of the Digital Layout, a multifunctional information system to store, analyse, process and visualise engineering data.
The project is not just about introducing a freestanding digital layout and 3D model of the refinery. The primary goal is to integrate the 3D model into daily business processes of the refinery. Future users of the product are not only the production asset reconstruction department employees, but also process engineers, mechanical engineers, maintenance planners and reliability experts. The original scope of work was extended during the project by introducing a refinery engineering data management system and developing an information standard. There are also plans to integrate the new system with the existing IBM Maximo maintenance planning system.
In 2021, 3D layout engineering data management systems were commissioned at AR and POCR, and the business process of using 3D was implemented.
KPI Digitalisation
Since July 2018, JSC NC “KazMunayGas” has been carrying out a project to build the first Kazakhstan Petrochemical Industries (KPI) gas chemical complex in Atyrau Region.
The polypropylene plant (KPI LLP) is the first phase of the Integrated Gas Chemical Complex (IGCC), which is scheduled for launch in 2021. Its capacity will be 500,000 tonnes annually. The second phase is the polyethylene plant.
KPI is a new industrial facility and there is an opportunity to build it as a fully digital asset from scratch.
Most of the major downstream and chemical companies (BASF, BP, ADNOC) have digitised their assets in stages over a long period of time. There are no examples of fully digitalised assets in Kazakhstan yet. KPI aims to reach the development level of Digitalisation 4.0. In the future, once basic automation and digital solutions are in place, the possibility of building a remote process control centre for IGCC to control the plant from Atyrau is being considered.
KPI will be digitised in two stages. The first stage is scheduled to complete in Q4 2021 (in sync with the launch date of IGCC). The second stage will begin after IGCC is commissioned.
The first stage (before the commissioning of IGCC) implements introduction of the following components and systems: instrumentation and controls, emergency shutdown system (ESD), distributed control system (DCS), maintenance planning system, LIMS laboratory information system, MES production supervision system, production personnel training automation (computer-aided simulators), 3D refinery model, complex SAP S4/HANA implementation includes not only the core modules (ERP), but also the planning system, integration with production systems (MES, LIMS) and maintenance planning systems, as well as implementation of a single digital window (business intelligence tool).
The goal of SAP S4/HANA implementation project is comprehensive implementation of the latest version of SAP system at KPI in terms of corporate and production modules. As part of the project, all business processes were designed based on global best practices and international experience for petrochemical assets, and a target organisational structure of the asset was developed based on best practices and benchmarking.
In addition to integration with internal refinery systems (MES, LIMS, IBM Maximo, EDMS), integration with external systems is also possible: ETI, client bank, zakup.sk.kz procurement system.
SAP Core modules were launched on 1 January 2021: FI, TR, CO, MM, SD, HCM. Accounting, procurement, controlling and human resources business operations are already managed in SAP system.
The second stage of KPI digitalisation includes implementation of an equipment reliability management system (APM system), introduction of advanced automation through Advanced Process Control (APC), and development based on SAP S4/HANA modules.
The implementation of digital technologies and solutions will improve IGCC’s business efficiency: minimise equipment downtime and production failures, reduce reject rates, increase labour productivity, reduce operating expenses (routine repairs, consumption of raw materials, chemicals, utilities) and increase income by improving product yields as a result of optimisation.